We are riveting together the tail cone box on our project, and came to a sticking point when trying to set the aft-most line of vertical rivets – the ones that hold the back end of the side skins to the rudder post assembly. We received the extra doubler plate to accomplish the Mandatory Service bulletin along with our kit, and dutifully constructed the tail post with it incorporated (BTW, the hardware list has not been updated, so you better have an assortment of AN3 bolts so that you can upsize those that need to be longer) in the assembly. All was fine until we tried to set those two lines of rivets – and found that the extra doubler interferes with the un-pulled rivets. If you try to cheat the rivets in by pushing the factory heads in while upsetting the rivet, the shank swells before you can get them flush – so that’s a No Go.
The instructions on the Service Bulletin appear to be for a completed airplane that already has these rivets in place, and I noodled over the problem for a few days before finally deciding that the only way to do this right is to remove the plate (fifteen bolts, all of the nuts inside the tail cone), then set the rivets, and then replace the plate – in essence, doing the mod as if it was a completed airplane. It would have been nice to know that before I fully assembled the tail-post….. Oh well!
We have the plate removed right now, will pull the rivets, then reinstall – that should finish up the tail cone box, and we can move on to the turtledeck.
This is with the doubler plate still in place, with all but one of the bolts removed. The rivet holes all line up with the center of the doubler, so it stops you from inserting the unpulled rivets fully:
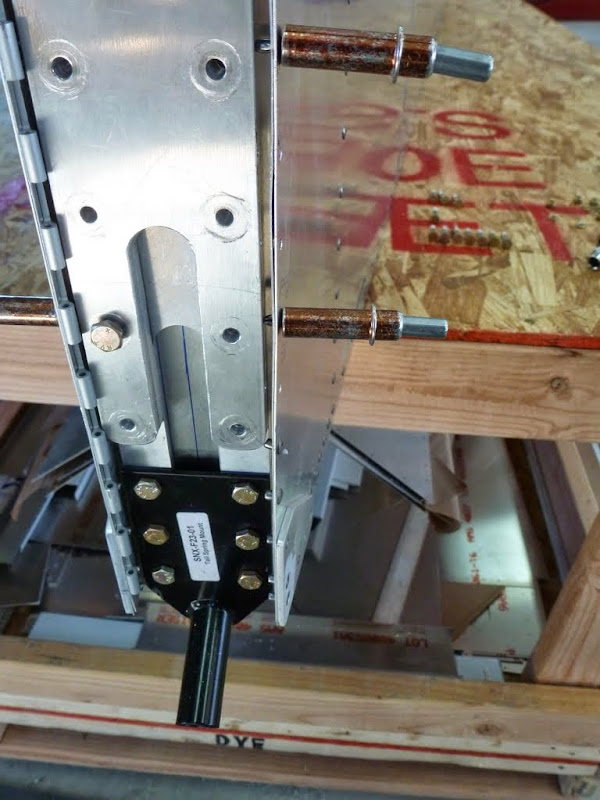
With the doubler plate removed, you can now see the tips of the clecos in the holes – and the rivets should insert fully before pulling:
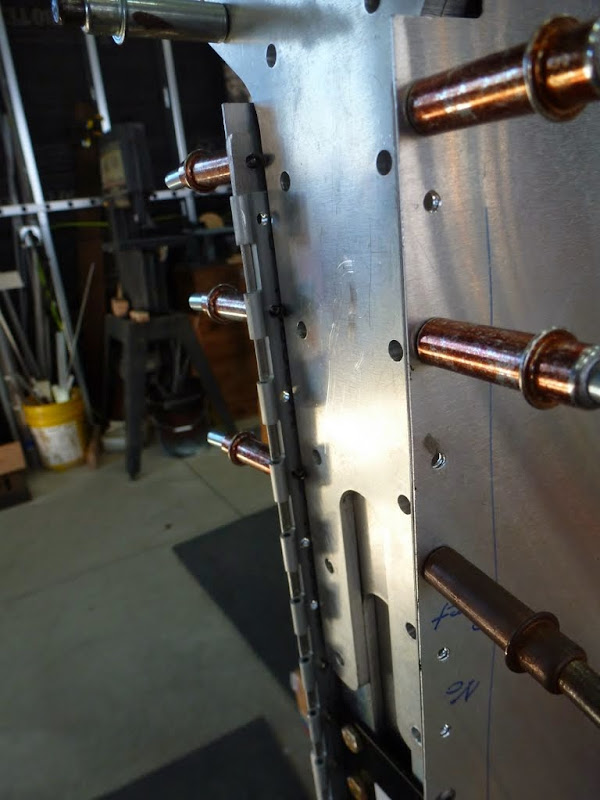
View looking down with the doubler plate removed – it is easier to see how the rivet holes line up with the plate in this view:
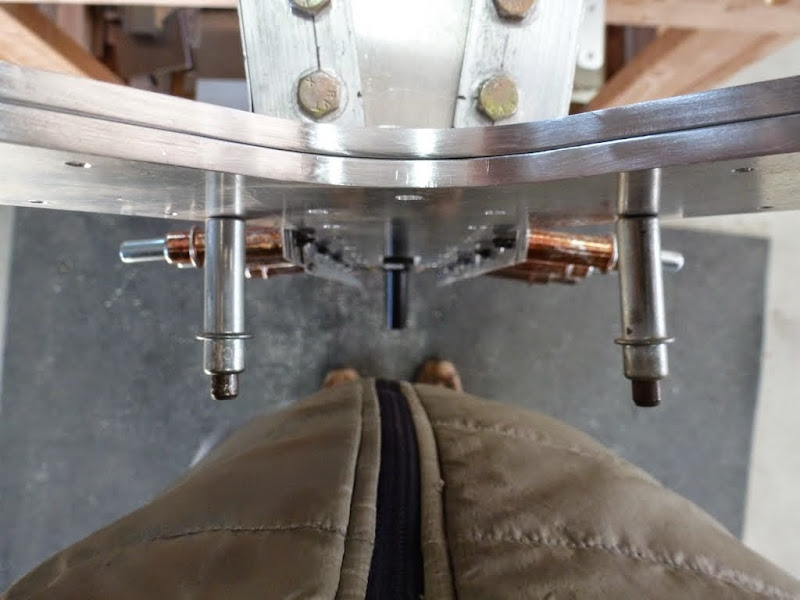
Hopefully, the pulled rivets won’t be so long as to interfere with getting the plate in place (the Service Bulletin instructions talk about prying the sheet metal out of the way to allow it to clear the rivets – we’ll see if that is necessary). I have considered squeezing solid rivets in those holes, as the shop head side would be shorter than with pulled rivets – but it looks like it will probably be OK with pulled rivets, and I think that the Cherry’s, with steel mandrels, are stronger than aluminum solids. This looks like an important area to get right!
Paul