Hi Guys,
A quick update on the VeeCU development.
For those that don't know, here is how I installed the injectors for development work. They are cheap Chinese injectors, intended for motorcycles I think, but they are sufficient for their purpose. In any event, pretty much a direct shot at the intake port.
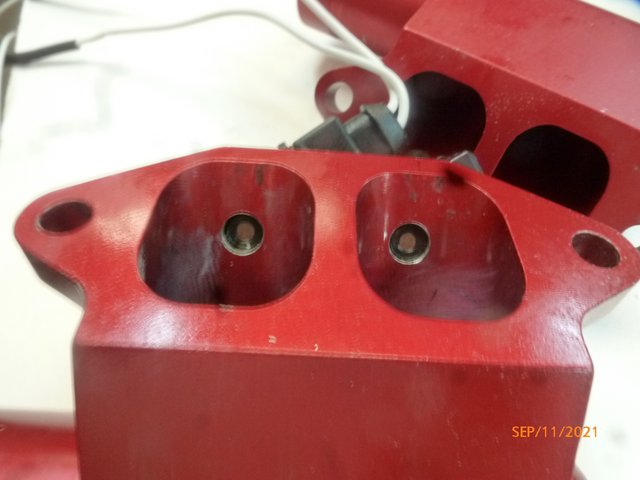
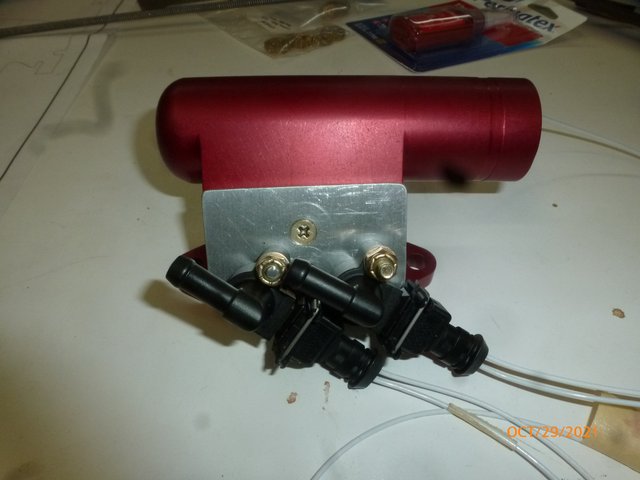
One of the primary reasons I wanted fuel injection on my VW is to protect my rear cylinder exhaust valves. My rear cylinders always lean out under high power causing me to have to reduce power, risk burning my rear cylinder exhaust valves, or run so rich on takeoff that power is again down. So, fuel balance is top of my priorities for fuel injection.
As for the VeeCU, I want it to be as simple and inexpensive as possible. So ..., no fancy/intelligent control head. That poses some challenges as far as the user interface is concerned. But, it forces me to think up simple solutions. And simple is good.
My first attempt at fuel trimming was to use a rotary switch to select a cylinder and then use the UP/DOWN switch to add or subtract fuel for that cylinder. That was a disaster. With no display it was way too easy to get lost, dazed, and confused.
Then it fully dawned on me that I wasn't trying to "Trim" the fuel, I was trying to "Balance" the fuel. That led to my second, and I think final, run at the user interface.
The rotary switch is a four position switch with two positions left of center and two positions right of center. What I have for engine instrumentation is a Grand Rapids EIS. It's a six cylinder unit that is too old to be updated to a four cylinder unit but it's what I have so I use it. I have wired the EGTs such that the readings match the cylinders if you stand up in the cockpit and look down on the engine.
Anyway, here is how the user interface for Balancing the fuel distribution ended up.
If you are trying to balance fuel on the left side of the engine, place the rotary switch one click left of center. If the EGT is high on the rear cylinder, click the UP/DOWN switch down, and here is the important point, that will add 1% fuel to the rear cylinder and subtract 1% fuel from the front cylinder. If you click the UP/DOWN switch up it will add to the front cylinder and subtract from the rear cylinder. Of course the right side works the same.
I presently have it such that if you turn the rotary switch all the way left and click up, it will add 1% fuel to the left pair and subtract 1% from the right pair. And similar on the right. I find this feature of limited utility and may remove it entirely. If you have bad balance left to right it's probably an intake leak or a clogged injector and you need to fix that.
Balancing the fuel this way never changes fuel flow, it just walks the EGTs into balance at whatever fuel flow you currently have. The sum of the trim percentages used to balance the EGTs is always zero.I was fooling around today with the new Balance method and took a couple of pics.
Just because I can :) You will notice the trim numbers sum to zero. Also notice that it didn't take much trim to match up the EGTs.
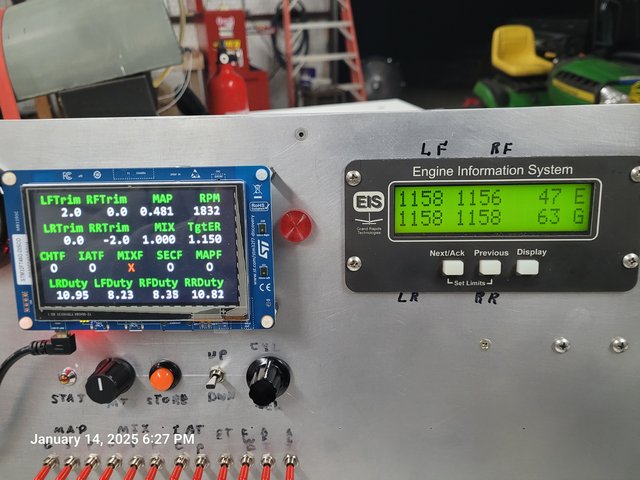
Until yesterday, I had never played with the leaning functions of the EIS. This pic shows the peak EGT spread lean of peak.
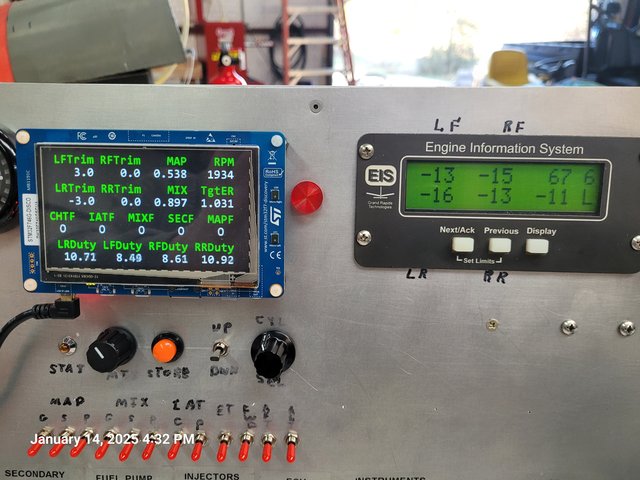
With the balance method described above it's easy to get the "Gami Trim" to near zero. Just lean until the first cylinder peaks, click on that cylinder to add fuel, and carry on in a similar manner until all cylinders have peaked.
The reason that it didn't take much trim to balance the EGTs in the previous pic is because the EGTs were balanced during engine calibration, at each calibration point, and the trim numbers saved as part of the calibration. In normal operation those trims numbers are interpolated keeping the EGTs balanced over the full RPM range. You might also notice the Duty Cycle difference on the last line of the display to see how much imbalance there was that is compensated for by the calibration data.
BTW, at low RPMs it takes as much as 25% to keep the front to rear EGTs balanced.
I've also implemented the Cold Start fueling. I finally found a method I liked and copied it. Here is a link to the method I copied.
Ref:
https://www.youtube.com/watch?v=jTL1OlmY3kUOne more test performed today was to run the engine to 2500 (the highest I'm comfortable with in the shop) and check the minimum secondary ignition voltage at which the engine ran smoothly on secondary alone. This test was performed at mixture points as lean as the engine would run smoothly and as rich as the engine would run smoothly. For both cases the engine began to miss just below 5 volts on the ignition coils.
Forever Forward,
Wes