Hi Guys,
I received the thermal conductive glue. A long time ago a guy showed me a method for measuring the temperature of an IC. First you get some high quality TC hookup wire. Then form a TC by stripping the wire and clipping off all but one strand of the wire. Next, twist the two strands together tightly and clip off all but the very tip. Put some thermally conductive "stuff" on the IC in question and stick the tip of the wire into it all the way to the surface of the IC. Make sure the strands do not touch outside the thermally conductive stuff.
That's all there is to it. A very responsive TC with very little heat sink effect.
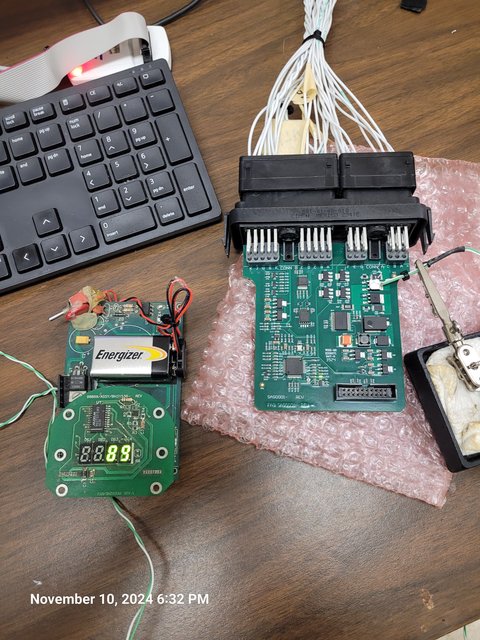
I have an old EGT prototype gauge that I rescued from the trash after a lab clean up at work some 25 years ago. Still works and is very accurate.
To test the ignition transistor temperature rise I decided to go for broke. I hooked up a 3 Ohm Dynatek coil and set the RPMs to 60. At 60 RPM no dwell control is applied/possible so the coil is powered virtually 100% of the time. I intend to rate the VeeCU for operation over a voltage range of 6 to 20 volts so I set the voltage to 20.
I got some results I didn't expect.
At the beginning of the test:IC Temperature 22 Deg. C.
Coil Resistance 3.0 Ohms.
RPM 60.
Voltage 20.
Current 6 Amps.
During the test peak IC temperature was 90 Deg. C.
At the end of the test:IC Temperature 81 Deg. C.
Coil Resistance Approximately 5.0 Ohms
Current 3.4 Amps.
I didn't expect that! I have been assured by Dynatek that the coil does not contain a ballast resistor. So I asked Cpt. Google what the "thermal coefficient of resistance for copper" is. It's about 0.4 percent per centigrade degree. You can run the numbers but an increase from 3.0 to approximately 5.0 ohms requires an increase of the order of 200 Deg. C. I knew the outside of the coils got hot but I wouldn't have suspected the primary winding got that hot. I don't know, but that's what it seems like. I've duplicated the results with two different makes of 3 Ohm coils. The 5 Ohm is probably a little low. I couldn't get the power off and the meter leads on the coil fast enough. Once the leads were in place you could see the resistance of the primary drop at about 0.1 Ohm per second. Like I said, not what I expected.
Here are a some more "stabilized" measurements.
RPM 4000
Voltage 20
IC Temp 70
Current 2.15 Amps.
RPM 3000
Voltage 14
IC Temp 52
Current 1.3 Amps
I reduced the Voltage to 6 volts to check the spark with a hot coil. At 6 volts the spark duration was 0.75 mSec.
I also checked a hot coil at idle and 14 volts.
RPM 950
Voltage 14
IC Temp 36
Current 0.45 Amps
Injector was about 0.14 A (MAP 500 mBar, Duty 5.5, Calculated FF .816 GPH)
So for a hot coil at Idle total current draw = (2 x 0.45) + 0.14
or about 1.1 Amp.
I'll test a 5 Ohm coil soon.
Live and Learn,
Wes