Page 1 of 2
Cowl inlet shape

Posted:
Sat Jan 05, 2019 5:59 pm
by lutorm
While the temps on our Aerovee are a lot better, and a whole lot more even across cylinders, than they were before we installed the custom plenum, we are still unable to climb for more than ~80s at Vy before the CHTs hit 400+F, and we can't really climb at less than maybe 110mph without eventually getting above that temperature. This might improve as the cylinders get more broken in, but one topic that I've been wondering about since getting the Sonex is the apparently-suboptimal inlet shapes in the cowling.
Basic aerodynamic principles say that inlets should have rounded lips and then a fairly gradual diverging shape on the inside. The Sonex cowl violates both of these principles for both the cylinder and oil cooler inlets. At least on our airplane, the openings have sharp edges without the slightest amount of rounding. I suspect the airflow into the inlets could be improved by giving them a rounded edge and an internal diffuser. The way the cowl fits, this is not straightforward, though. I was wondering if anyone's already experimented with altering the shapes of the inlets.
Although now I'm looking at pictures on the Sonex web site, like
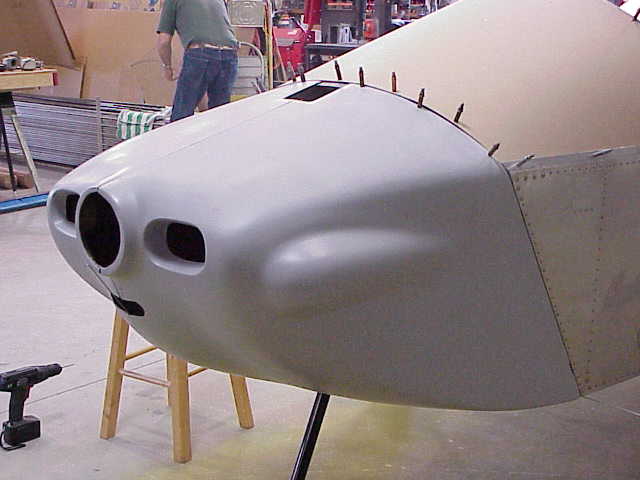
that appears to have rounded edges. Maybe the openings on our cowl were cut too large? Or has the design been changed? I don't have a picture of it handy. The oil cooler inlet seems to still have a sharp edge though.
Re: Cowl inlet shape

Posted:
Sat Jan 05, 2019 6:47 pm
by Bryan Cotton
I had considered bonding in some foam and making a better inlet, but that project has been moved to the "extra credit - after first flight" category.
Re: Cowl inlet shape

Posted:
Sat Jan 05, 2019 8:40 pm
by Brett
.......
Re: Cowl inlet shape

Posted:
Sat Jan 05, 2019 11:08 pm
by gammaxy
There's definitely been talk of adjusting the lips, but I doubt it's your problem. I didn't do it. My exit is also sized according to the plans. For things like this, I used the philosophy to build according to plans despite what I read on the forum and make changes according to experiments during Phase I.
I'm following your plenum experiments with great interest, but I'm doubtful what you're currently seeing is meaningfully different than the stock intake on my airplane. Three cylinders peak at about the same mixture setting with the front left peaking a little later.
I can easily climb at any speed above ~85mph in Alabama summers without exceeding ~375F. It also tends to take 4-5 minutes or so to get that hot. Sounds like you can barely get to pattern altitude before worrying about temperatures? Are all your cylinders that hot?
Are you sure the rubber on the baffles are sealing against the cowl all the way around? You have great attention to detail and the rest of your baffles look great, but it's the only obvious thing that comes to mind. Have you considered checking the ignition timing? Does power/temperature change significantly between primary & secondary? What kind of propeller RPM and climb rate are you getting at Vy? I get about 2850rpm which I understand to be a little low and climb around 650fpm (~950lbs).
Re: Cowl inlet shape

Posted:
Sun Jan 06, 2019 1:11 am
by wlarson861
Have you tried taking off and climbing to pattern altitude and shutting off the electronic ignition and then continuing the climb? If this gives lower temps then the ignition timing is off. If it makes no change then investigate other issues. Ignition timing is the most common issue in hot engines.
Re: Cowl inlet shape

Posted:
Sun Jan 06, 2019 5:18 am
by lutorm
Thanks for these pointers. I have tried shutting off the secondary and did not notice anything obvious, but it was not a highly controlled experiment. I will definitely try this again in a more controlled fashion. I do know that I get a larger RPM drop at 2000RPM when shutting off the secondary than I do with the primary, and that I think indicates that the secondary may be further advanced.
On the last flight we tried a Vy climb at 70MPH (from sea level), with 2 people so likely just over 1000lbs. Full throttle was 3150-3200 RPM and the climb rate about 600fpm. (This is the standard Aerovee Sensenich prop.) After 90s of that, the rear cylinders broke 400F while the fronts were 380 and 390. Oil temp had hit 205F. OAT was about 85F. (I'm surprised that you have such a good climb rate with only 2850rpm. I wonder if any of our readings, either RPM or climb rate, are off...)
It's quite possible that the baffles are not sealing well, I've attempted to check this but not seriously. I'm not sure what the best way is? The temps in the cowl do seem lower than I would expect if all the air had gone through the cylinder and head fins, the temperature probe on the plenum shows about 140F. The baffle seal is the standard "D" seal that comes with the fence baffles, not the wide silicone strips I've seen used on some Sonexes.
Re: Cowl inlet shape

Posted:
Sun Jan 06, 2019 1:35 pm
by gammaxy
Sounds like me and my friends are pretty heavy--we'd definitely be pushing 1100lbs. You've got quite a friend to be willing to fly 2 up on a 3d printed plenum. There's enough uncertainty in my numbers and density altitudes, etc., that I'm pretty confident you are generating more power than me. I wouldn't be surprised if my 650fpm was actually at 900lbs, etc. If you haven't noticed already, the under-wing location for the static pressure port isn't ideal--it's easy the apply a little nose-down pressure during climb out to give yourself an extra 100+fpm indicated temporarily, so you really have to be careful to get good measurements.
I think Vy is closer to 75mph in my plane and the climb rate rolls off gradually and I have no obstacles so I tend to climb on the faster side of Vy around 80-85mph.
I checked my RPM numbers with a laser and they are accurate. I probably just need to get a new propeller. But then that extra ~6hp might have me chasing engine temperatures too :-)
I get different ~50 RPM drops on the ground at 2000RPM than in level flight at full power (almost negligible and seems to be a little different from flight to flight), so I wouldn't draw any conclusions from that until you've done it in the air.
I know the top of my back baffles don't seal perfectly, especially where the piano hinge is on the vertical split cowl. Once you've flown it a bit, you can look at the cowl and baffles to see where they have marks and discoloration indicating they are sealing.
I've always flown with the oil cooler on top which seems like it would allow the engine to cool a lot better. I wonder if you could block off the oil cooler's cowl opening for a short flight to see if it makes a difference? This time of year in Alabama it gets so cold that I tape off about 3/4 of the oil cooler anyway. Not sure I'd try it if it was in the 90s outside.
Personally, I'm interested in how the Sonex B models now vent out the sides of the cowl. I suspect this would make a big difference. Not sure if anyone's posted comparisons.
Hope I haven't distracted too much from the point of this thread. I do remember people adding fiberglass behind the top of the inlets and I'm pretty sure people have done something similar on RVs.
Re: Cowl inlet shape

Posted:
Tue Jan 08, 2019 3:54 am
by lutorm
gammaxy wrote:You've got quite a friend to be willing to fly 2 up on a 3d printed plenum.
He's the original builder/CFI... But yeah, we now have almost 10h on the engine since the rebuild, and more than that on the plenum from ground runs before we rebuilt it, so I guess people have convinced themselves that it's not going to just come apart. I'm still making a rev B to tweak the design a bit, and that one will be reinforced with a layer of fiberglass to minimize any long-term creep of the material.
Re: Cowl inlet shape

Posted:
Tue Jan 08, 2019 9:08 am
by Darick
I had issues with cylinder temperatures getting into the 400's right after take off. As soon as #1 cylinder got to 420 I leveled off and reduced RPM to keep temperatures down. I couldn't get the small black factory cowl seal to make good contact so I switched to the red silicone from ACS, which solved the problem. See the August 17, 2018 entry in my photo album.
Re: Cowl inlet shape

Posted:
Tue Jan 08, 2019 12:17 pm
by Gordon
RV Inlet Ramps Info............
Just for the record (for any non RV builders).......
All RV cowls have a ramp that you must glass in to the "top cowl" air inlet to smooth out the air flow. That fiberglass piece (ramp) is the width of the air inlet and about 8" long so as to give a nice smooth flow of air.
At the bottom side of that air inlet there is an aluminum piece or ramp that mates the "bottom lip" of the inlet to the front cylinders so the air makes a nice smooth transition into the cowl.
On all my RV's I had to add an "air dam" to the front cylinders to keep them from running too cold......that is pretty much standard practice on all RV's with a Lycoming.
Gordon.......Hummel 2400...Onex.....(RV Repeat Offender)