Hi Guys,
The list is a little slow today so I'll jabber some.
For those interested in EFI:
The genesis for the VeeCU was the podcast :
http://www.sonexflight.com/58/index.html . It's very interesting and informative. Highly recommended. It got me fired up :-)
When I first started down this road I bought any and every book I thought was relevant to EFI.
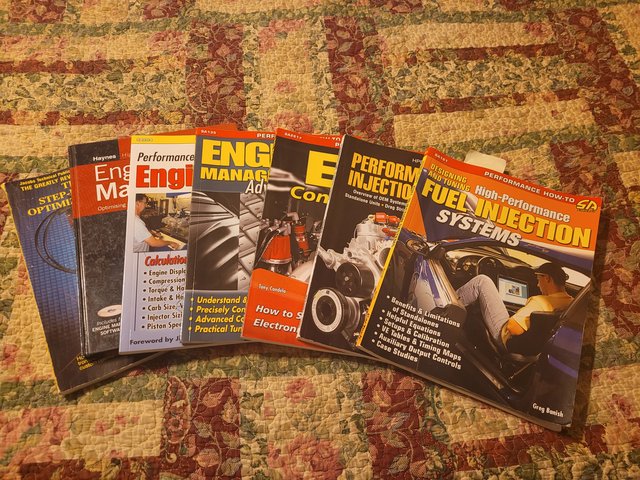
Some of them are useless, some are OK, and one is excellent.
If you are interested in EFI I highly recommend this book.
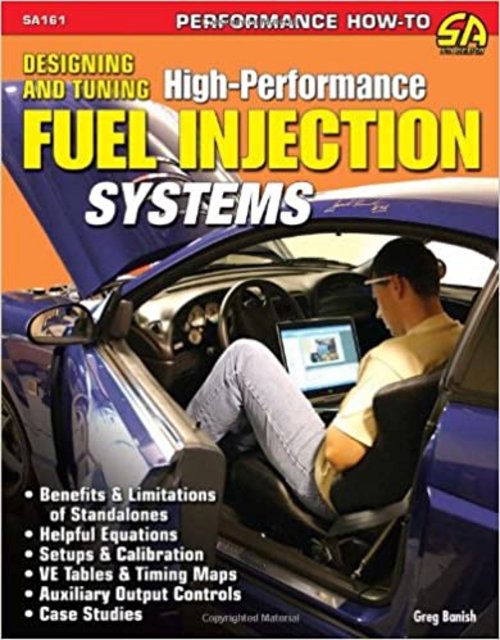
The author is an OEM tuner by day and a performance tuner by night. An easy read and mixes theory and practice of engine tuning nicely.
As for the VeeCU project, I've been working on memory layout. I'm keeping things as simple as possible. As of right now here is what an engine tune will look like. It won't format right when posted, but you get the idea.
eTuneTypeDef eTuneType; // Version of the tune template.
char cTuneName[80]; // The name ex. "High Compression Hummel 2400".
uint16_t u16TotDisplacement; // Total displacement in cc.
uint16_t u16ComRatio; // Compression ratio * 100.
bool bIsTurboed; // True if turbo charged.
uint8_t u8AltPPR; // Alternator pulses per revolution.
int16_t as16RPM [RPM_POINTS]; // RPM break points for the VE and Spark tables.
int16_t as16Spark [RPM_POINTS]; // Ignition advance at RPM points.
int16_t as16VE [RPM_POINTS]; // Volumetric efficiency at RPM points.
int16_t as16EngTemp [TEMP_POINTS]; // Temp break points for warm up enrichment.
int16_t as16CSEnrich [TEMP_POINTS]; // Enrichment Pcnt. * 10 for warm up enrichment.
int16_t s16Cyl1Trim; // Percent * 10 Trim for cylinder 1.
int16_t s16Cyl2Trim; // Percent * 10 Trim for cylinder 2.
int16_t s16Cyl3Trim; // Percent * 10 Trim for cylinder 3.
int16_t s16Cyl4Trim; // Percent * 10 Trim for cylinder 4.
uint16_t u16FuelPressure; // Fuel Pressure regulator in mBar.
uint16_t u16FuelCutRpm; // RPM for over speed fuel cut.
uint8_t u8PrimerSize; // # of cyl fills for primer pulse.
uint16_t u16APSens; // Sensitivity of Accel Pump.
The unit can store any number of tunes.
For you C afficionados, anything I forgot?
Oh yea, I spoke with Peter Van Schalkwyk and he said he didn't have a throttle position sensor on his second SDS EFI VW aircraft and he didn't notice any difference with out the accelerator pump function. For starting, he said if the engine didn't fire immediately he would use the mixture knob to add more fuel.
Wes.